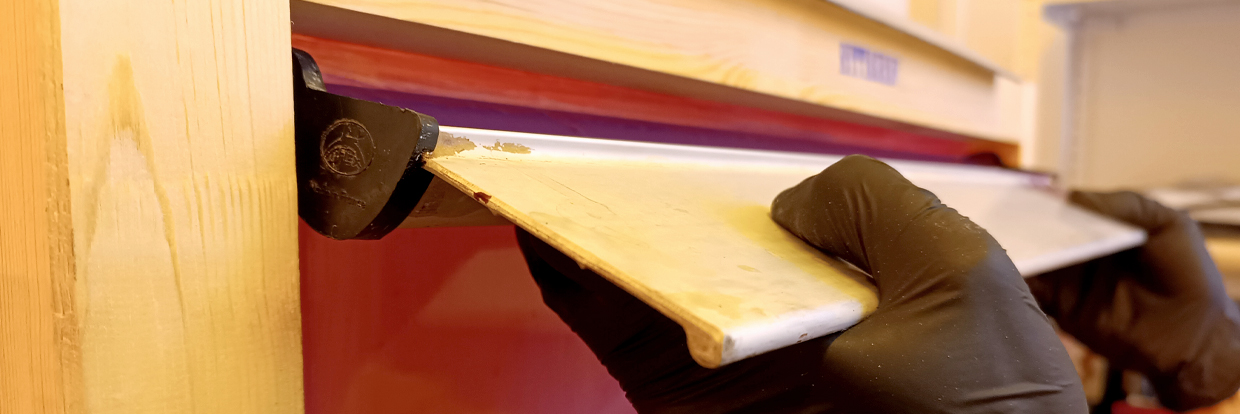
® Carlos Alguacil para Rittagraf
Para una excelente impresión en serigrafía es necesario atender la calidad del positivo o fotolito, trabajar con una buena emulsión y realizar una exposición adecuada. Pero la manera de emulsionar una pantalla de serigrafía influye mucho más de lo que creemos.
Preparar la malla antes de emulsionar
Antes de ponernos a emulsionar, es importante que la malla de la pantalla de serigrafía esté preparada para recibir la emulsión fotosensible. Es imprescindible que el tejido haya sido desengrasado y esté totalmente seco. Para conocer más detalles sobre cómo preparar y desengrasar una pantalla de serigrafía, recomendamos visitar este tutorial sobre el desengrasado de pantallas y tejidos de serigrafía.
La raedera: una herramienta adecuada para aplicar la emulsión de serigrafía
La herramienta que usamos para emulsionar se conoce con el nombre de raedera, canaleta o emulsionador.
Una raedera es una cubeta metálica donde alojaremos la emulsión fotosensible de serigrafía y que servirá para aplicar una capa uniforme de emulsión. Este tipo de cubeta suele ser de aluminio o acero inoxidable, tiene una disposición tubular en forma de V o U y tiene unas tapas laterales que contienen y evita que la emulsión se desborde. El filo que va a estar en contacto con la malla, debe de ser totalmente romo. Entre otras cosas, el grosor y ángulo del perfil del emulsionador determinan el grueso de emulsión que se va a depositar.
Las hay que contienen uno o dos filos. El filo de la raedera o emulsionador estarán en contacto con la pantalla y es necesario que siempre esté limpio. Un resto de emulsión o una muesca en el filo nos provocarán líneas o diferencias de gruesos de emulsión en nuestra pantalla.
Por descontado, las aristas de la herramienta, deben tener los cantos romos. Un emulsionador con los cantos o perfiles angostos puede romper la malla de las pantallas.
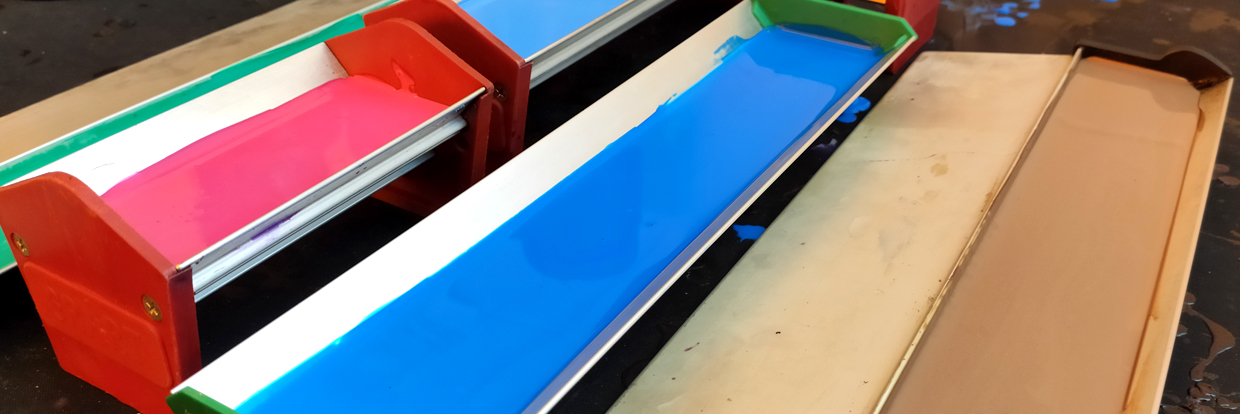
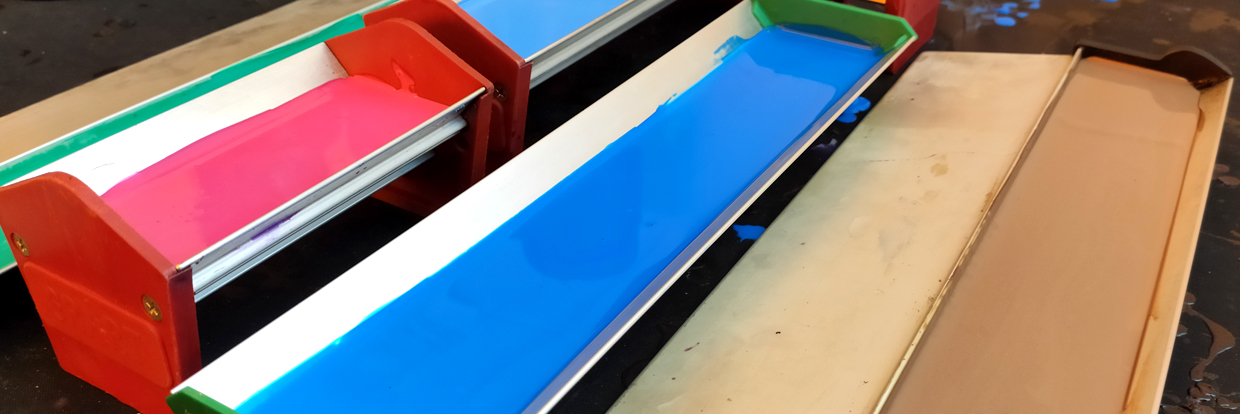
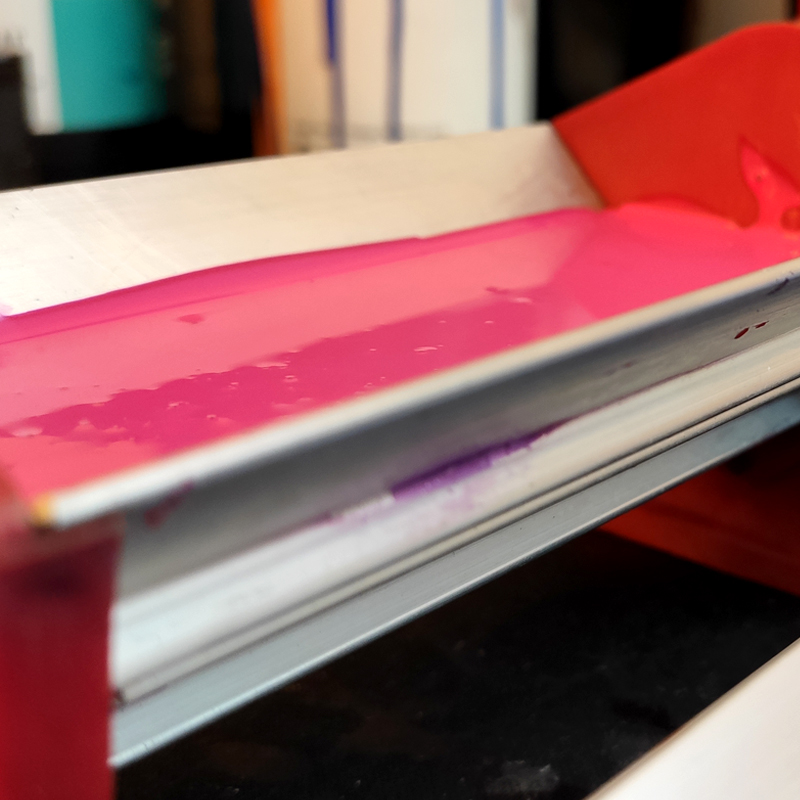
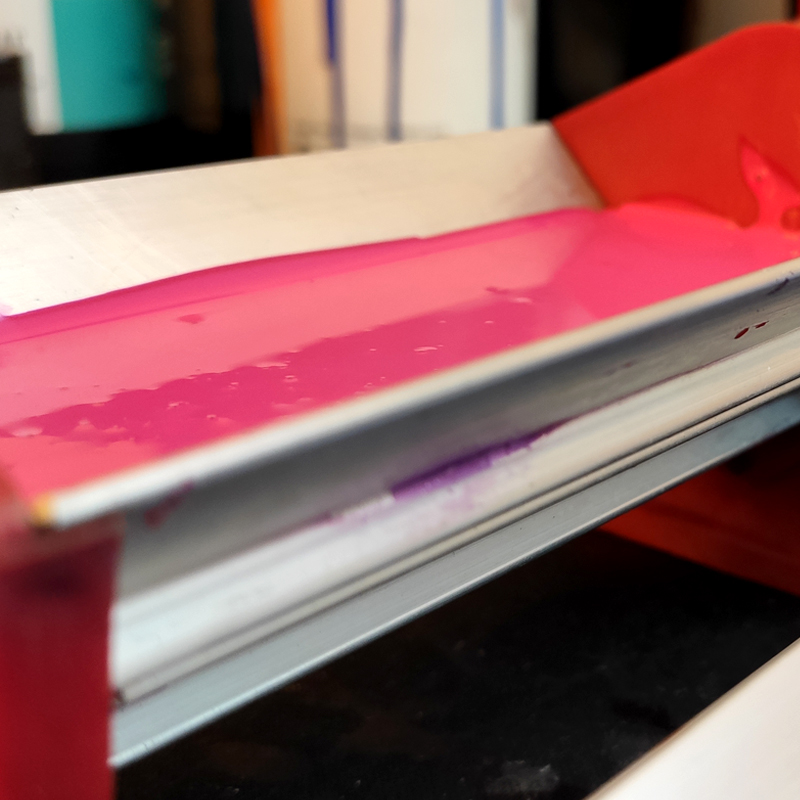
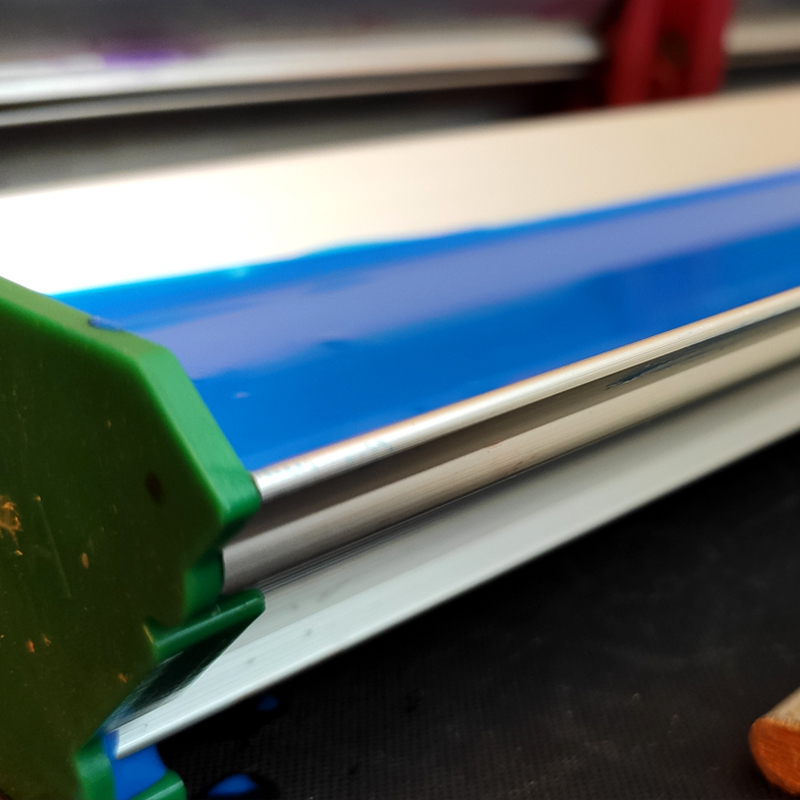
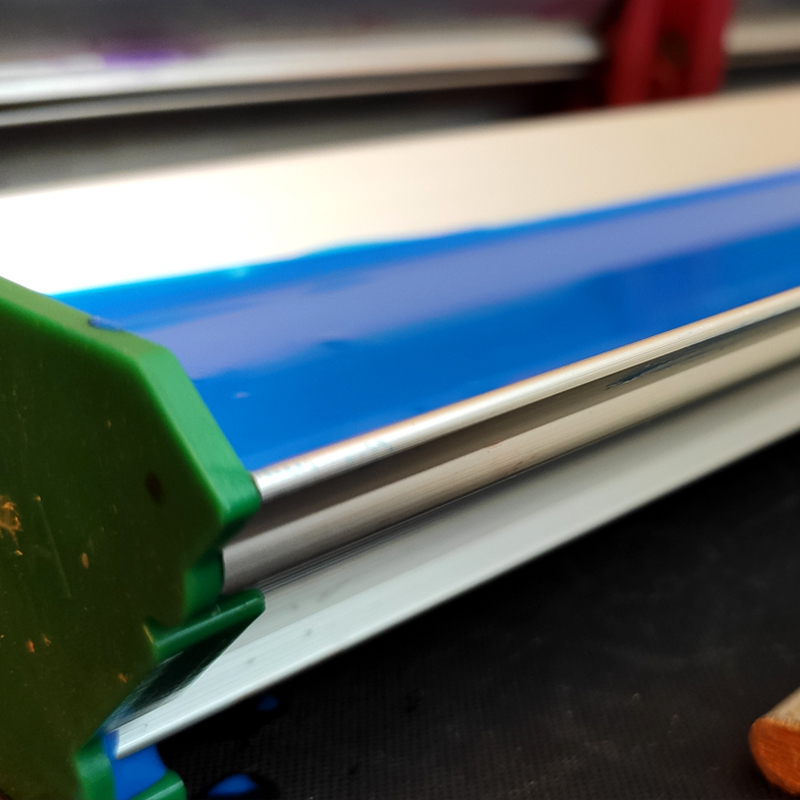
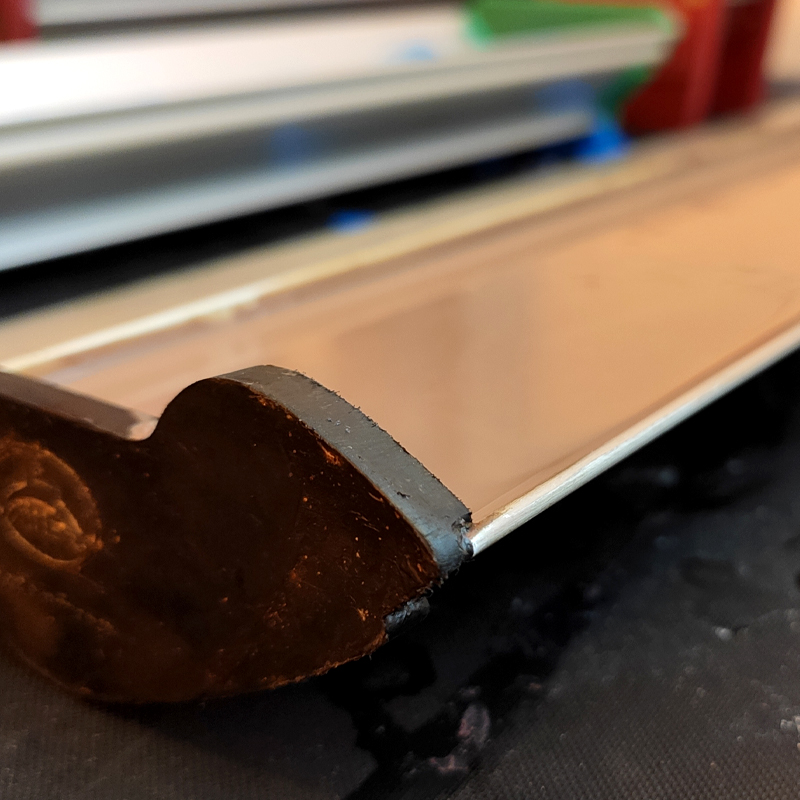
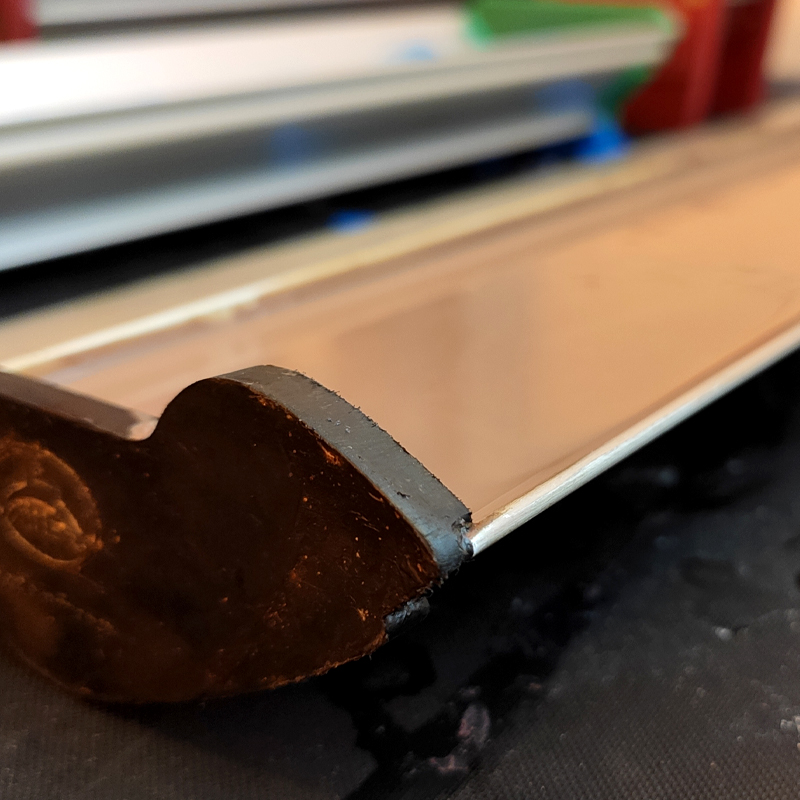
Escoger el tamaño del emulsionador de serigrafía
Necesitamos buscar una raedera del tamaño adecuado para la pantalla que queremos emulsionar. Siempre debe ser unos centímetros más pequeña que el tamaño interno de la pantalla. Si la raedera es muy justa, necesitaremos aplicar una presión excesiva y corremos el riesgo de romper el tejido en los laterales.
El emulsionador puede ser mucho más pequeño pero nunca debe ser más ancho que el tamaño interno del marco. Lo más recomendable es que el emulsionador sea entre 2 y 5 cm más pequeño que el marco. De esta manera, aprovecharemos al máximo el espacio de trabajo de la pantalla. Lógicamente, el ancho del emulsionador marcará el ancho de imagen que podremos grabar.
El cuarto oscuro o laboratorio donde emulsionar
No hay que olvidar que las emulsiones de serigrafía son fotosensibles y reactivas a la luz UV. Hay que evitar a toda costa cualquier tipo de intrusión de luz natural directa o indirecta en el espacio que vamos a utilizar para emulsionar. Las radiaciones UV del sol son justamente las que buscamos reproducir con nuestras insoladoras de serigrafía. Basta con pocos segundos de luz directa del sol para estropear cualquier tipo de emulsión de serigrafía.
Aunque no lo parezca, la mayoría de luces artificiales también producen pequeñas cantidades de ondas de luz que pueden estropear las emulsiones. De modo que también debemos evitar emulsionar cerca de fuentes de luz artificial directa.
Nuestro espacio para emulsionar y manipular pantallas de serigrafía debería estar exento de ventanas y fuentes de luz natural, manipulando nuestras emulsiones lejos de luces incandescentes, fluorescentes o incluso luces led. Las condiciones idóneas para un laboratorio de serigrafía sería conseguir un espacio preservado totalmente de luz blanca, usando luz roja o amarilla para mejorar la visibilidad. Este tipo de iluminación no afecta a los materiales fotosensibles y permite trabajar con seguridad de no estropear las emulsiones. La luz amarilla permite mejor visibilidad que la roja. Podemos conseguir bombillas y fluorescentes amarillos o bien teñirlos con laca especial para bombillas. Para los fluorescentes existen fundas amarillas para este cometido. Montar un pequeño laboratorio de serigrafía nos permitirá trabajar con mayor seguridad. Mejoraremos el emulsionado ya que podremos ver lo que estamos trabajando, sin miedo a estropear el material fotosensible.
Aún y así, como comentaremos más delante, pueden conseguirse resultados muy profesionales sin necesidad de tener un laboratorio serigráfico. basta con tener las precauciones de manipulación os vamos a ir exponiendo.
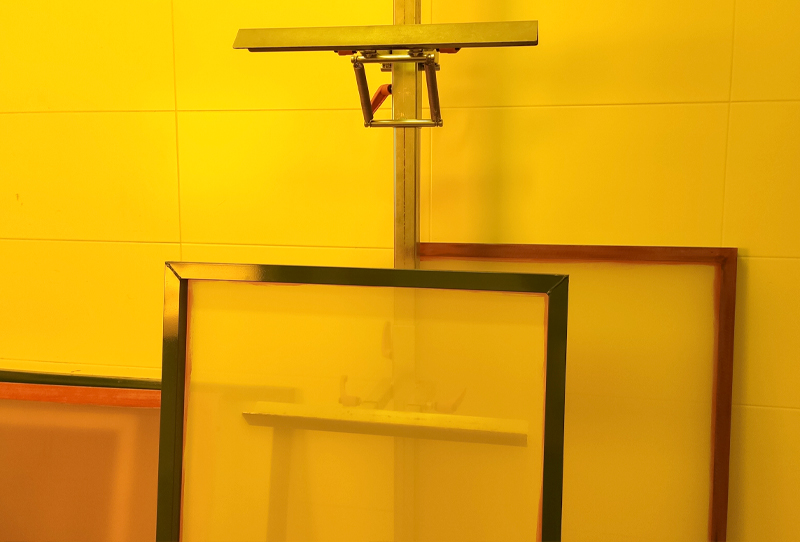
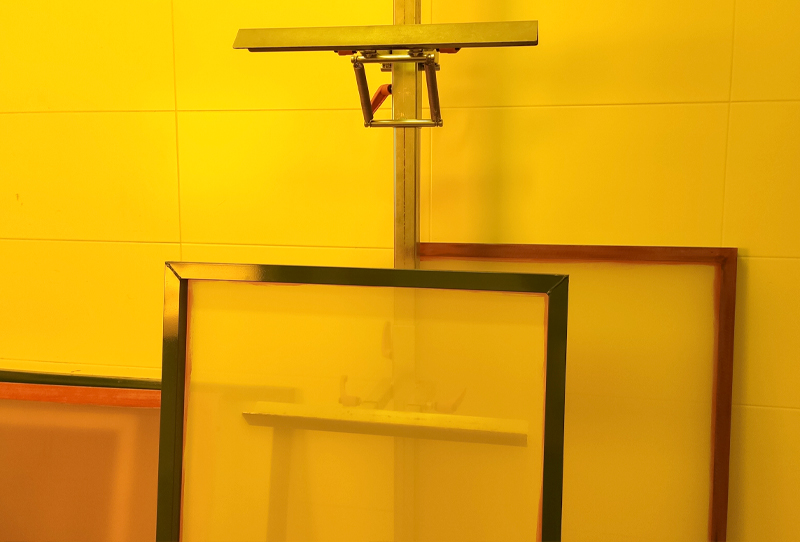
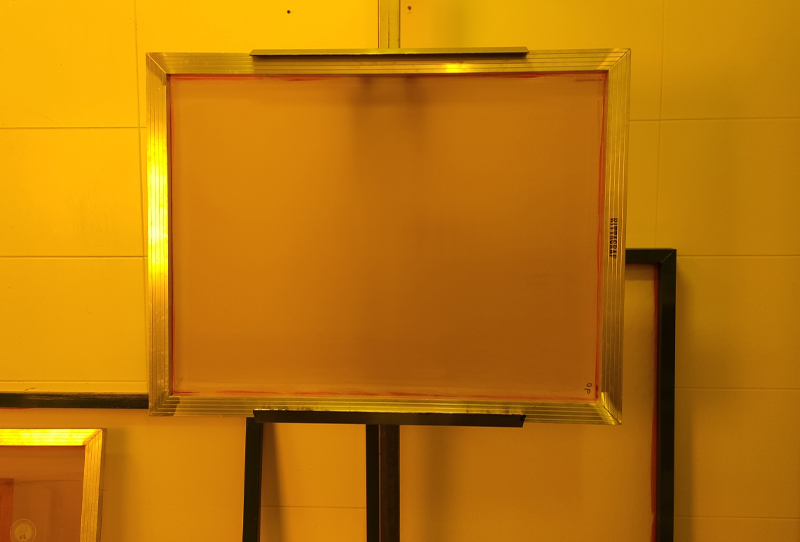
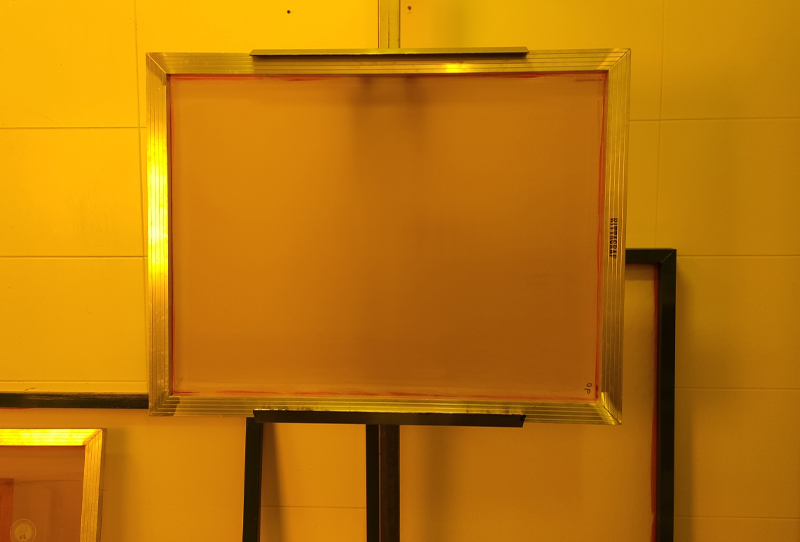
Preparar la emulsión de serigrafía antes de emulsionar pantallas
Preparamos la emulsión de serigrafía:
- Si se tratara de una emulsión de 1 componente: removemos bien y esperamos a que desaparezcan las burbujas de aire.
- Si se trata de una emulsión de diazo: Si aún no la hemos activado, debemos mezclar el diazo con el resto de la emulsión siguiendo las instrucciones del fabricante. Antes de emulsionar, debemos esperar, al menos 1 hora. Aunque es preferible esperar 24 horas. Nuevamente: sigue las instrucciones del fabricante.
Una vez la emulsión está preparada y no presenta burbujas de aire, vertimos una buena cantidad de la misma sobre la raedera o emulsionador. La emulsión debe cubrir al menos la mitad de la cavidad del emulsionador. Cuando aplicamos la emulsión no debe haber burbujas de aire. Así que si aparecen burbujas provocadas por el vertido en la canaleta de emulsionar, debemos eliminarlas con aire a presión (soplando) o con una espátula limpia (haciendo movimientos suaves a lo largo del emulsionador).
Cómo usar la raedera y emulsionar pantallas correctamente paso a paso
Aquí explicamos el uso correcto de la raedera, canaleta, bloqueador o emulsionador manual. Detallamos paso a paso cómo emulsionar una pantalla de serigrafía de forma correcta para obtener los mejores resultados y mejorar nuestro trabajo.
Paso 1: El emulsionador en contacto con la malla
Para emulsionar, debemos sostener la pantalla en posición vertical. Podemos hacer uso de alguna herramienta que nos ayude a mantener esta posición (estación de emulsionado) pero también podemos hacerlo manualmente.
Comenzamos emulsionando siempre por la parte exterior de la pantalla (lado de impresión) y acabamos por la parte interior del marco (lado de la racleta). Debemos hacer esto porque el mayor grueso de la emulsión debe de estar en la cara externa. Necesitamos que el grueso de emulsión quede en la cara donde debe depositarse el grueso de la tinta, la que estará en contacto con la superficie.
Si utilizamos una herramienta o alguien nos ayuda a sujetar la pantalla, podremos coger la raedera con las dos manos. Esto sería lo más recomendable. Si no disponemos de ayuda, podemos sostener el marco con una mano mientras manejamos la raedera con la otra.
Colocamos el filo de la raedera o emulsionador en contacto con la parte externa de la pantalla. Una vez colocado el filo sobre la pantalla, inclinamos la raedera a unos 45º mirando hacia abajo, hasta que la emulsión toque la pantalla. La mayoría de las tapas laterales de los emulsionadores marcan este ángulo.
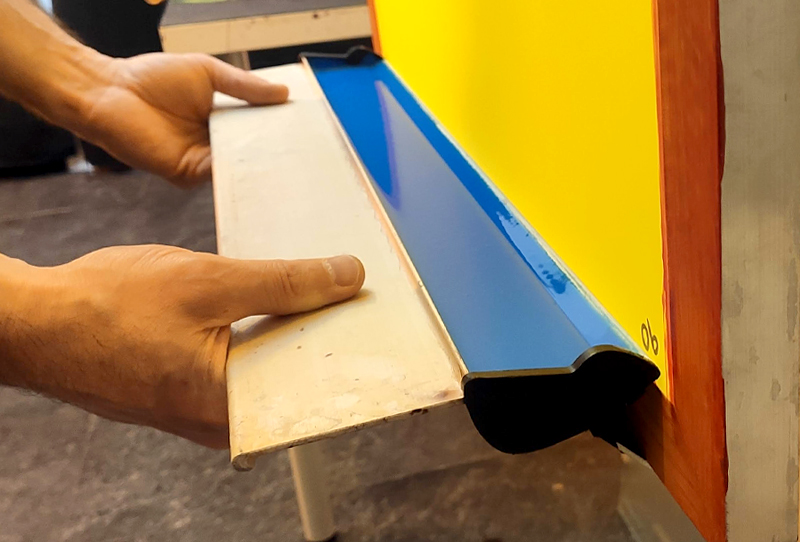
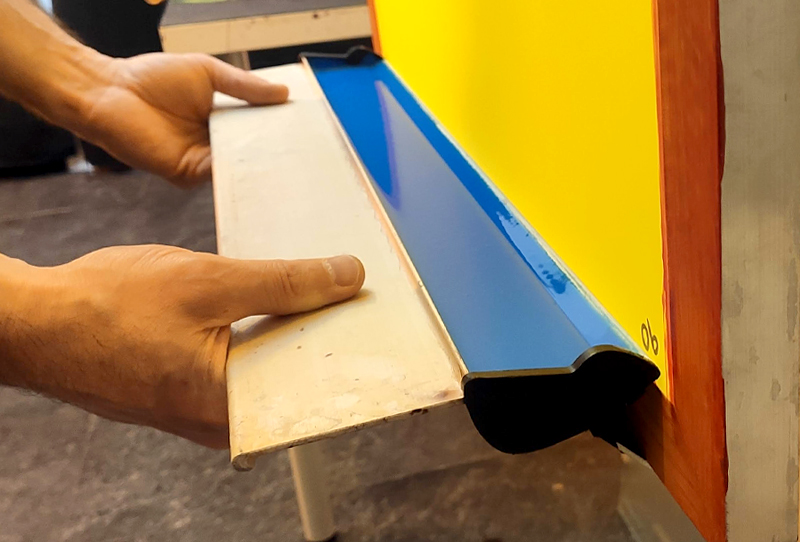
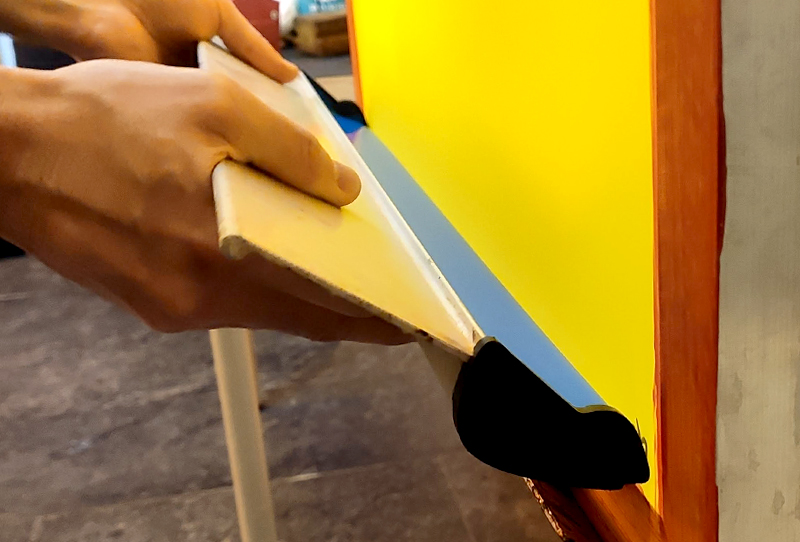
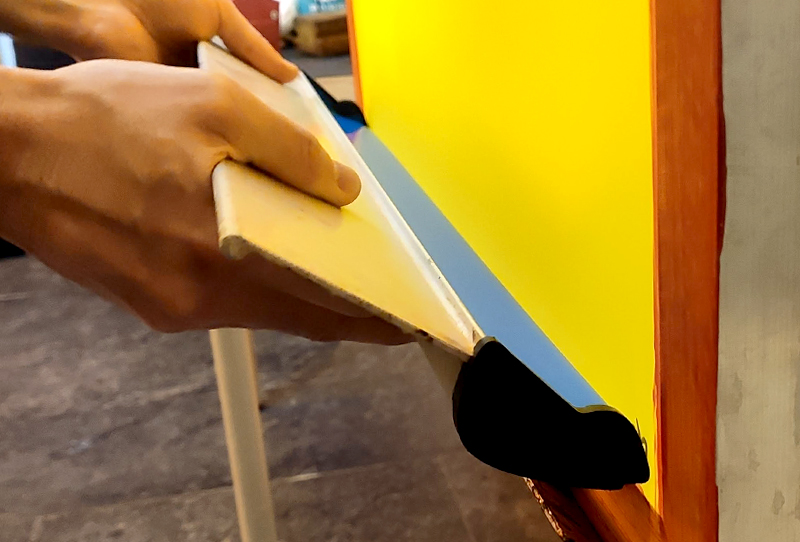
Paso 2: Presionamos y subimos
En el momento que la emulsión toca la malla de la pantalla a lo largo de toda la raedera estamos preparados para emulsionar. Presionamos la raedera y subimos a lo largo de la malla siempre manteniendo la misma inclinación y velocidad. No es conveniente correr demasiado pero tampoco es bueno subir excesivamente lento.
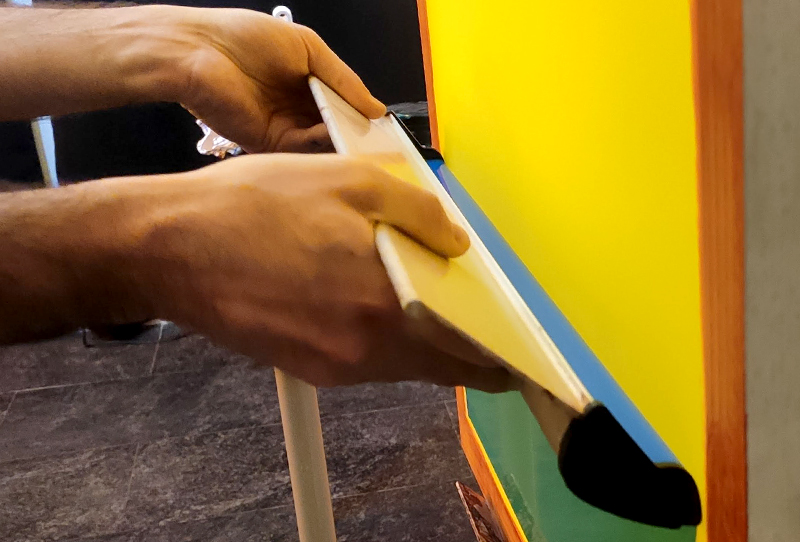
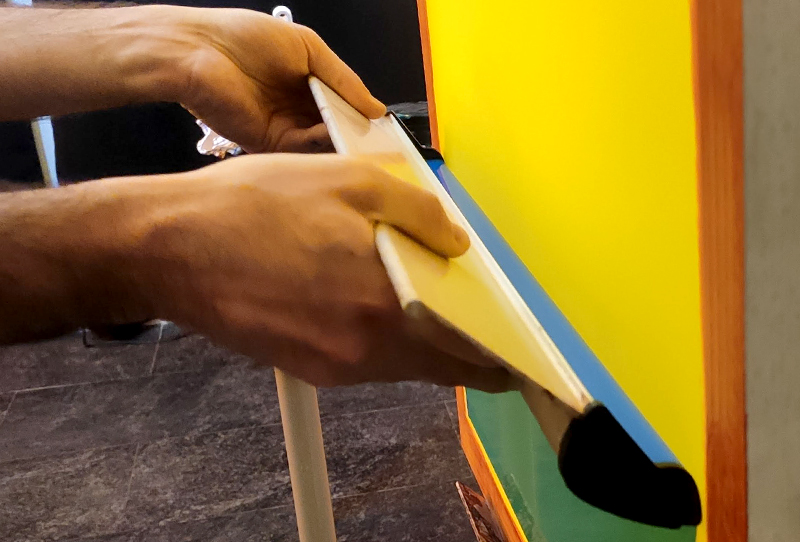
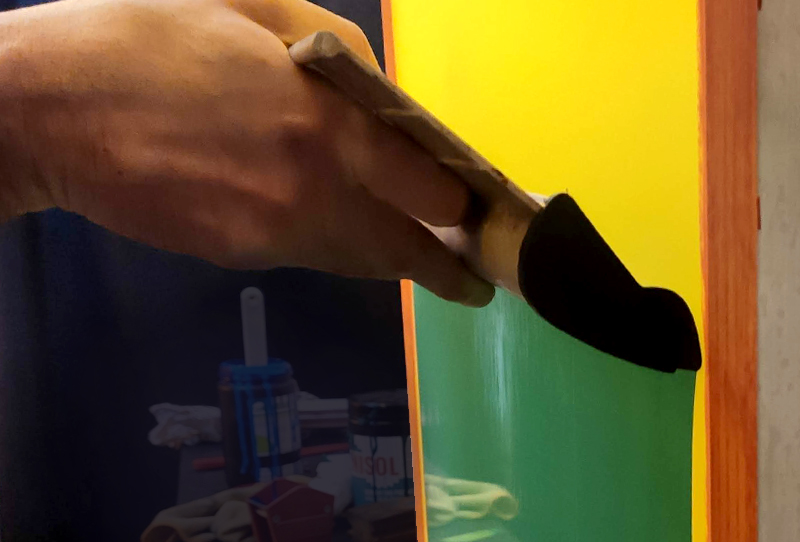
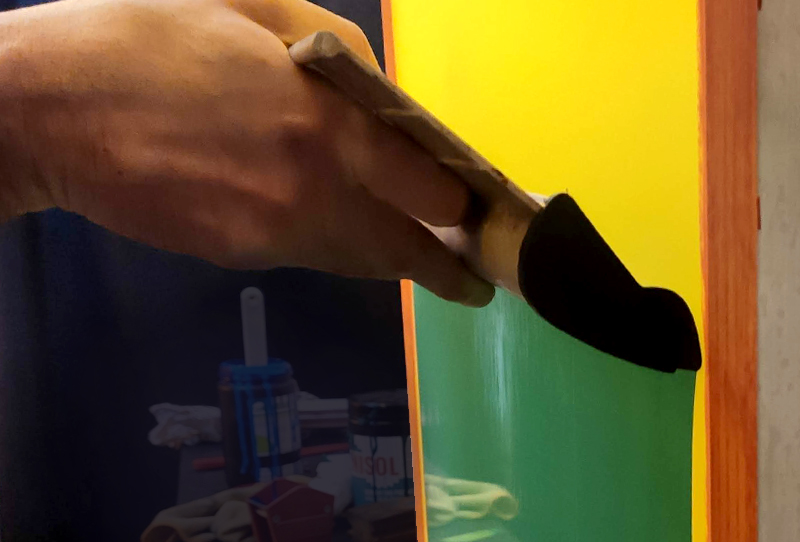
Paso 3: Inclinamos y cortamos el flujo de emulsión
Cuando lleguemos arriba de la malla, sin sobrepasarla, giramos la raedera hacia nosotros, hasta que la emulsión deja de estar en contacto con la malla. De manera que podamos separar el emulsionador sin que vierta emulsión.
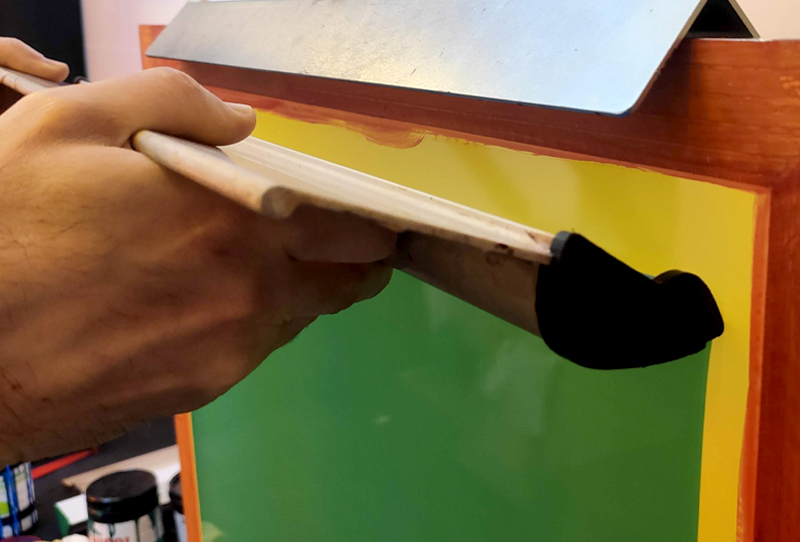
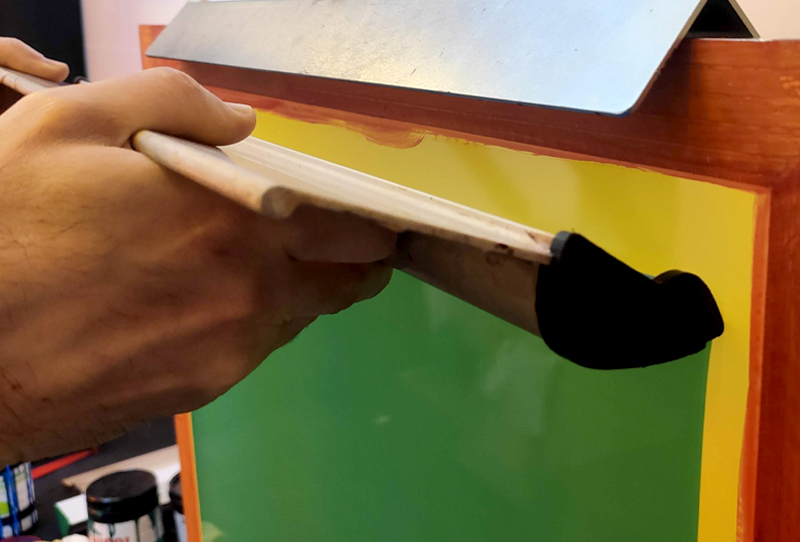


Paso 4: Repasamos y bloqueamos las zonas exteriores
Si nos han quedado zonas de la pantalla sin emulsión, como los bordes laterales, podemos emulsionar estas zonas con una raedera muy pequeña o incluso con una tarjeta de plástico de canto romo. Este paso evita el uso excesivo de cintas adhesivas industriales.
Es imprescindible que la emulsión refleje una capa fina y uniforme. Si han quedado restos o gruesos de emulsión, podemos eliminarlos con una espátula o una tarjeta de cantos romos. También podemos hacer pasar la misma raedera pero con la inclinación de +/- 45º mirando hacia arriba para recoger los excesos.
Paso 5: Capas de emulsión. ¿Cuántas deben hacerse?
Hay muchos aspectos a tener en cuenta a la hora de decidir la cantidad de capas de emulsión de serigrafía que vamos a aplicar; estos son alguno: la abertura de la malla, el grueso del perfil del emulsionador, la fluidez de la emulsión, la velocidad del emulsionado, el ángulo y la presión del emulsionado.
Todos los fabricantes ofrecen consejos de uso de sus emulsiones en las fichas técnicas. Por normal general, 1 capa de emulsión ofrece resultados pobres, siendo 1+1, 2+1 y 2+2 las más recomendables y habituales.
Teniendo en cuenta todas las variables anteriores, nosotros recomendamos hacer 3 capas de emulsión en húmedo: 2 capas exteriores + 1 capa interior. O como mínimo hacer 2 capas: 1 capa exterior + 1 capa interior.
Aunque no es una práctica habitual en talleres de impresión manual, se puede experimentar aplicando 1 capa de emulsión por el lado de impresión después del secado. De esta manera se asegura la cobertura del tejido.
Es importante estandarizar este proceso porque cualquier variable en la aplicación de las capas cambiará nuestros tiempos de exposición.
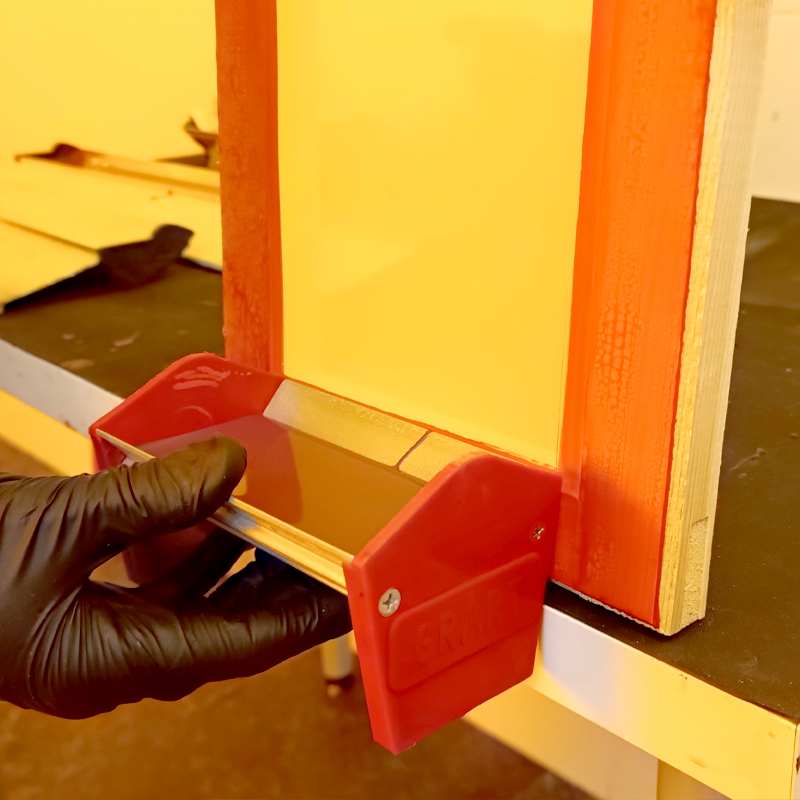
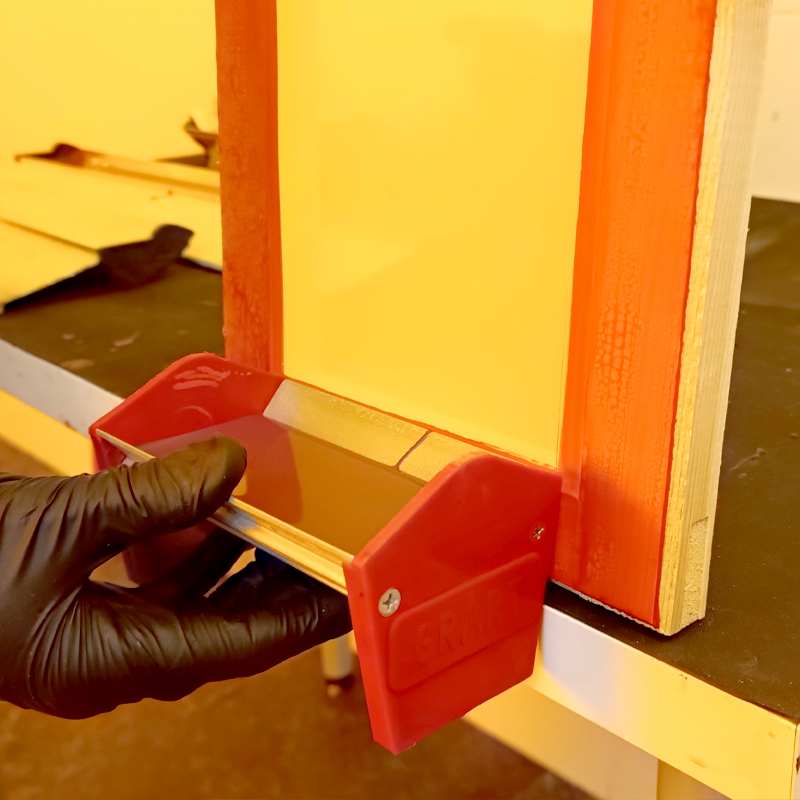
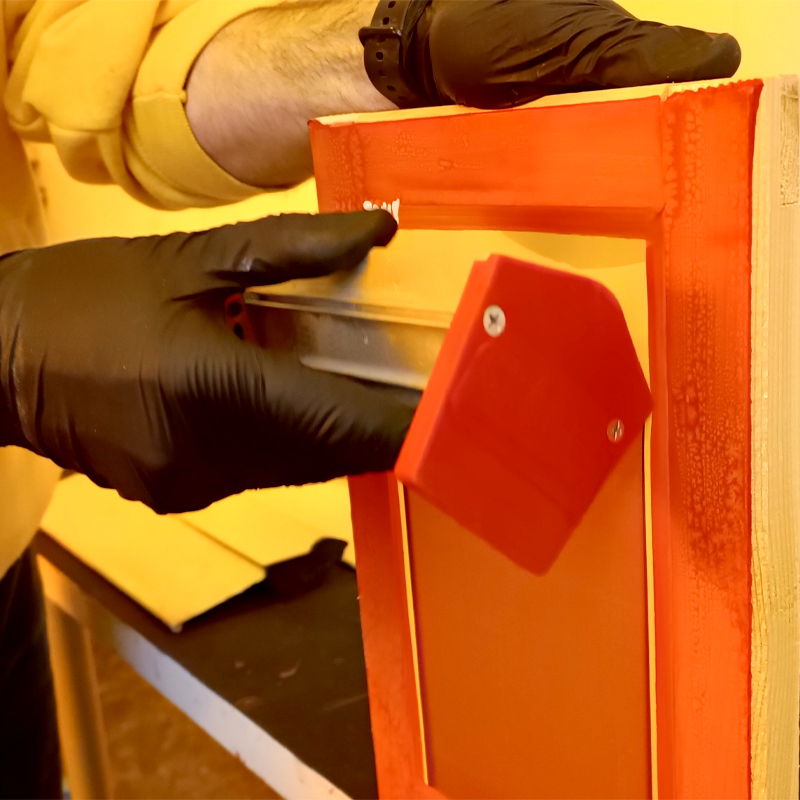
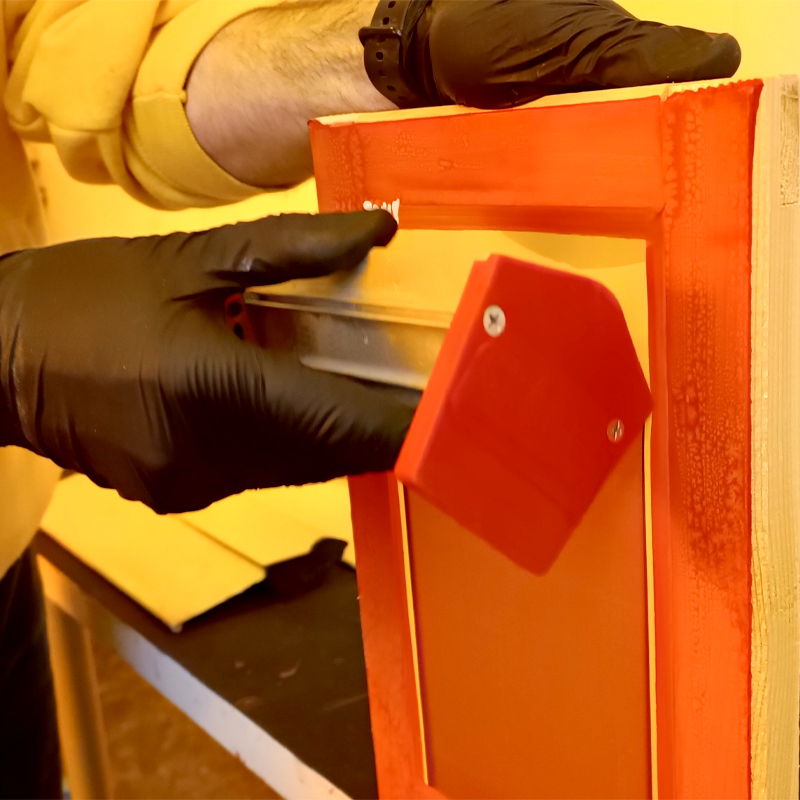
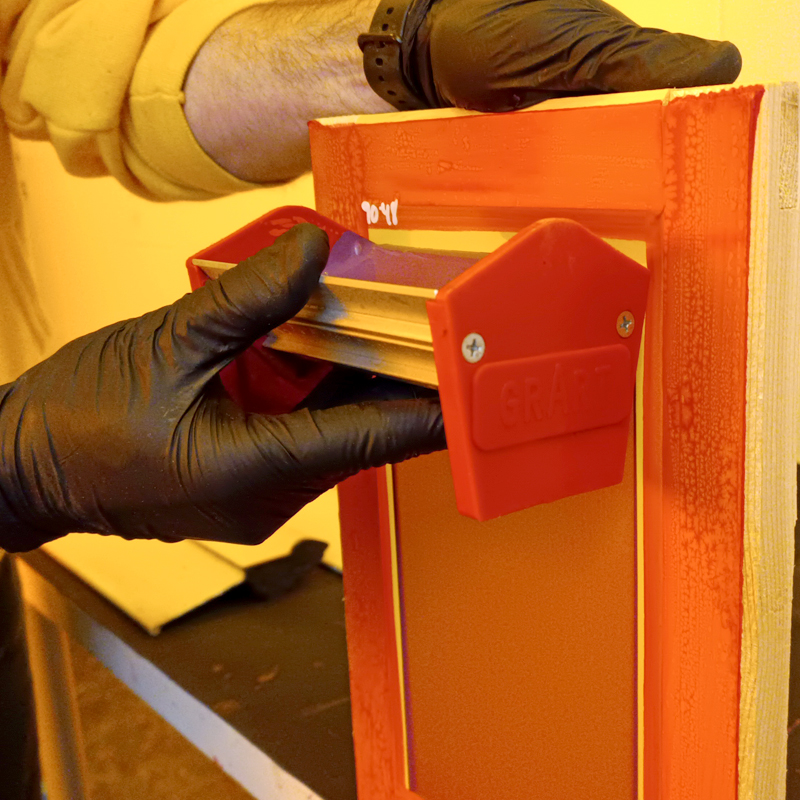
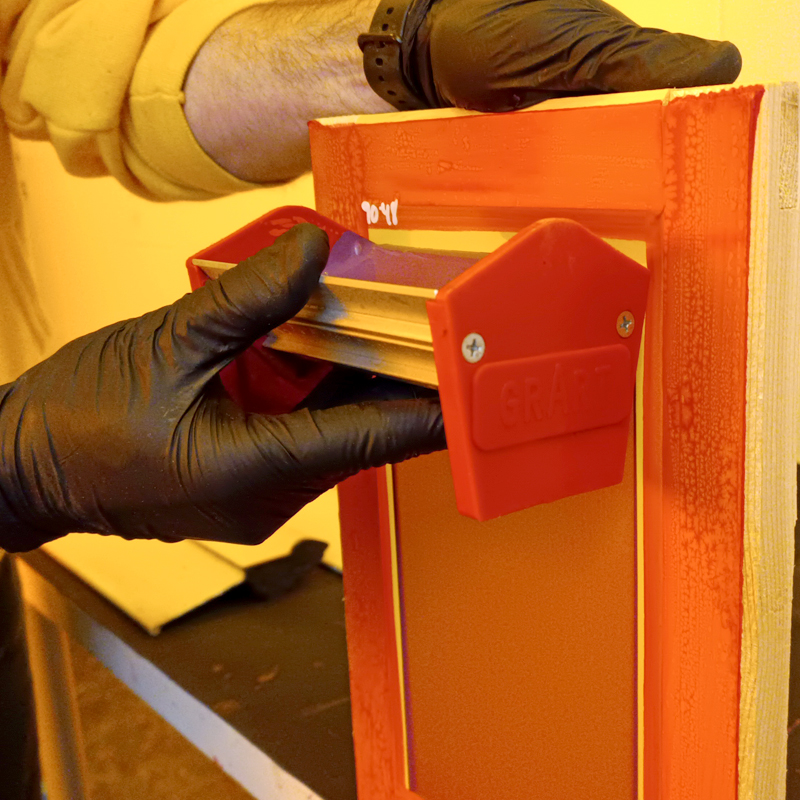
Primera capa de emulsión por la cara exterior de la pantalla (cara de impresión)
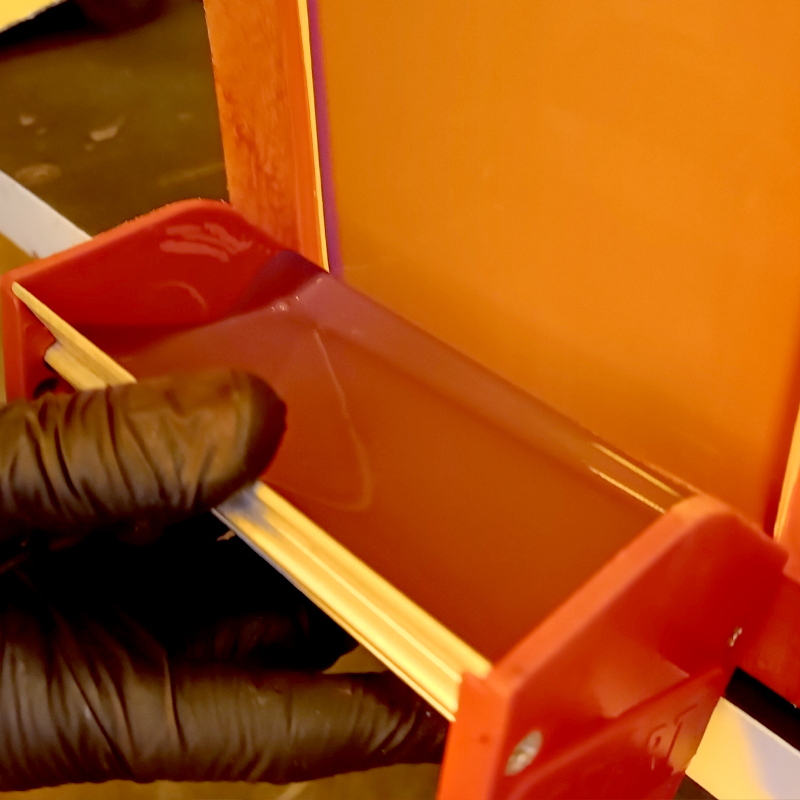
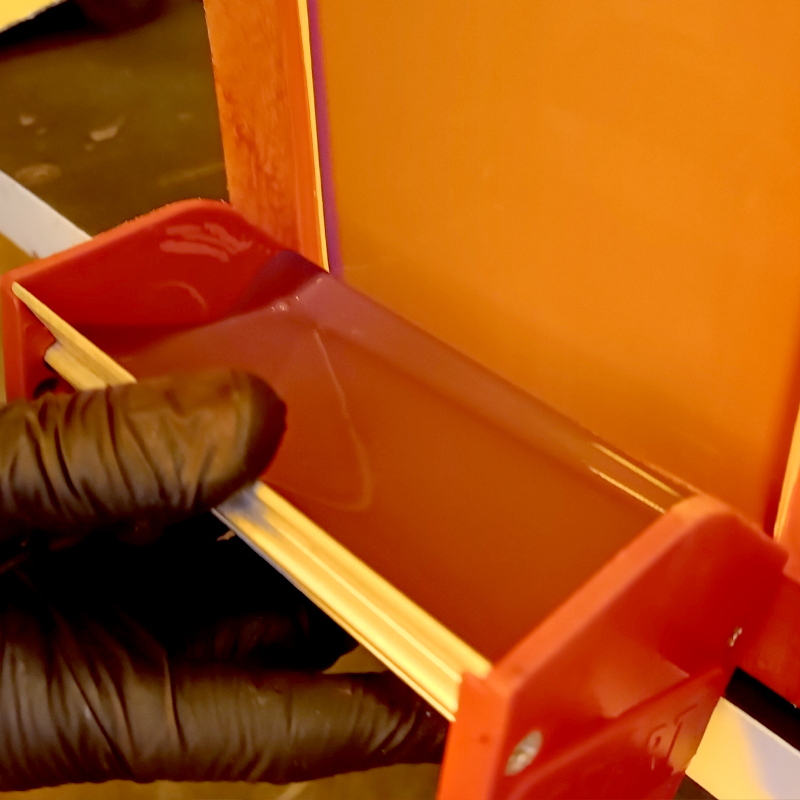
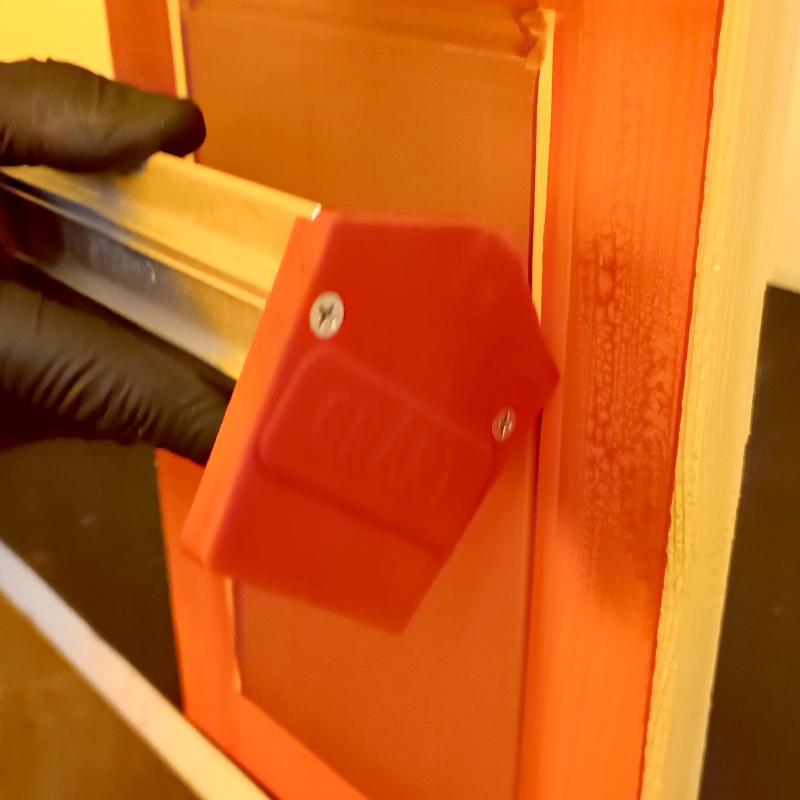
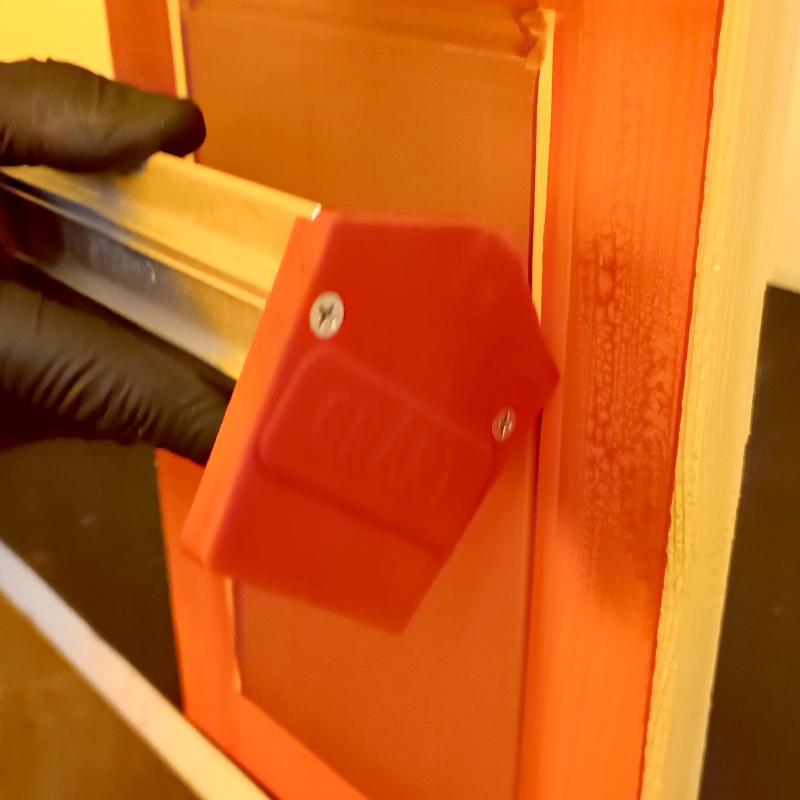
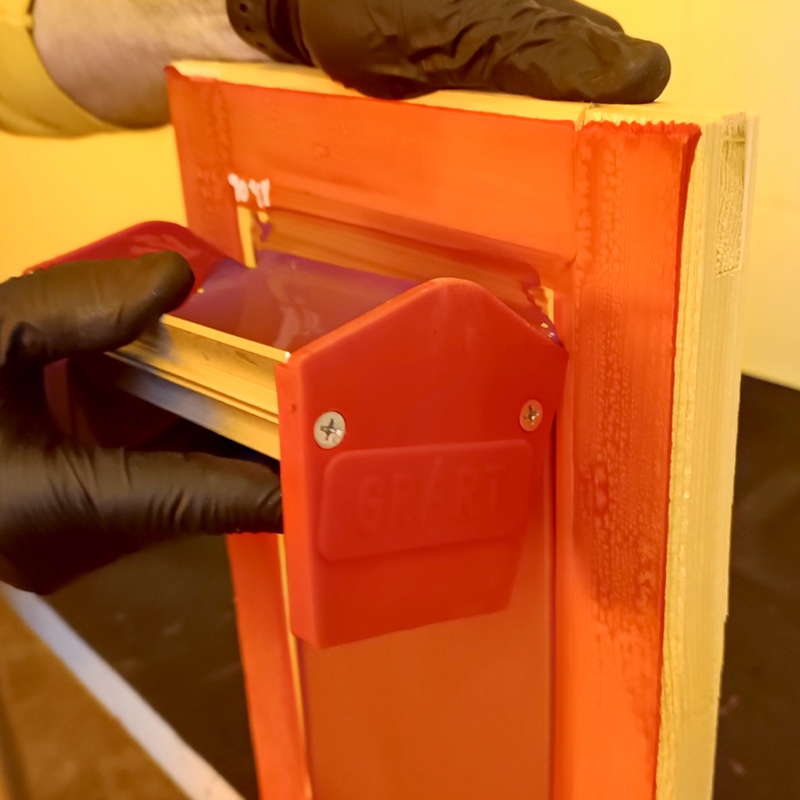
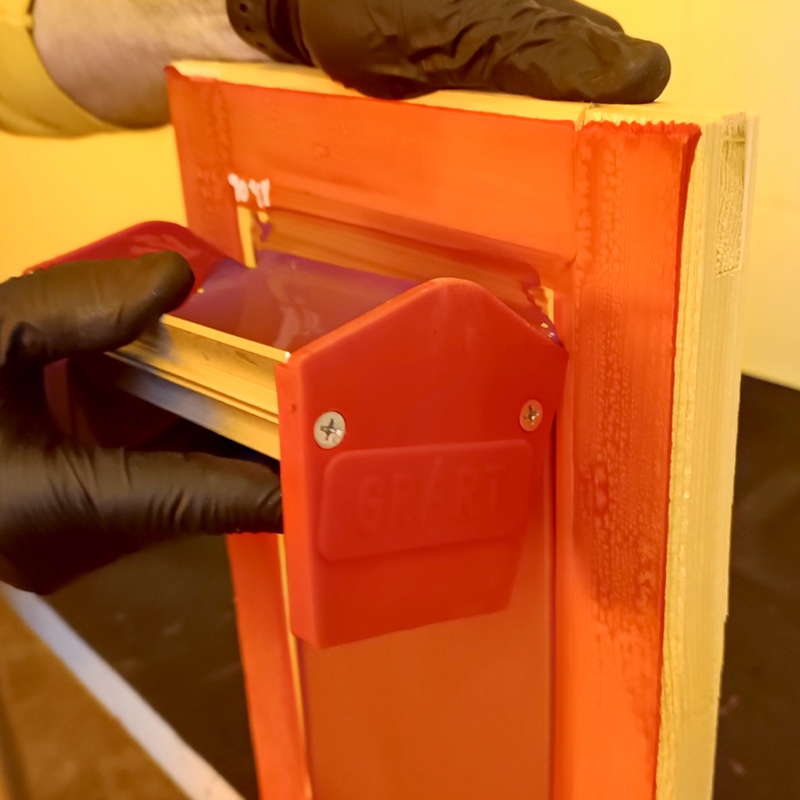
Segunda capa de emulsión por la cara exterior de la pantalla (cara de impresión)
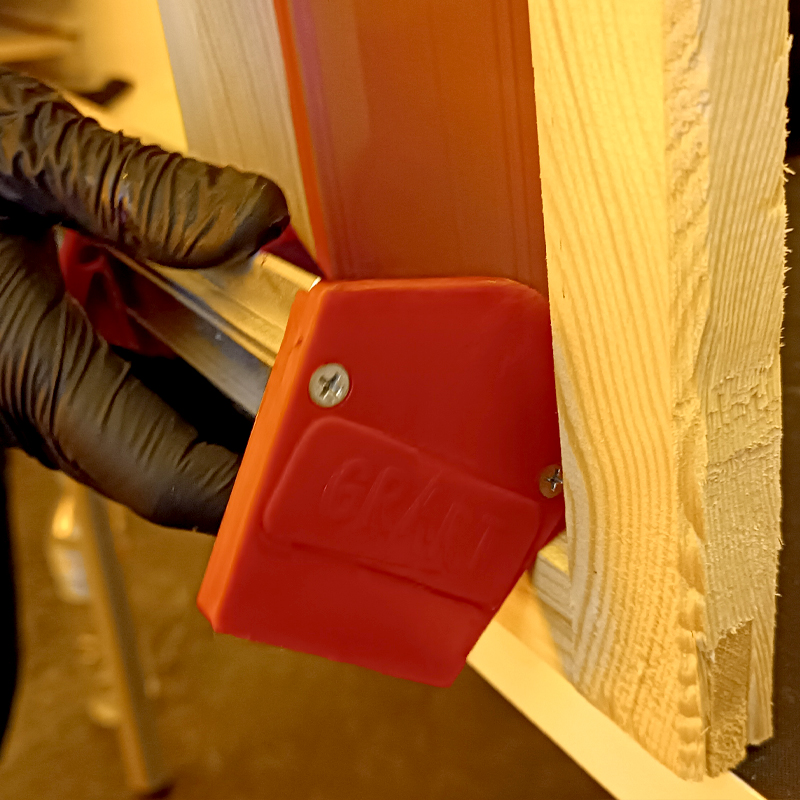
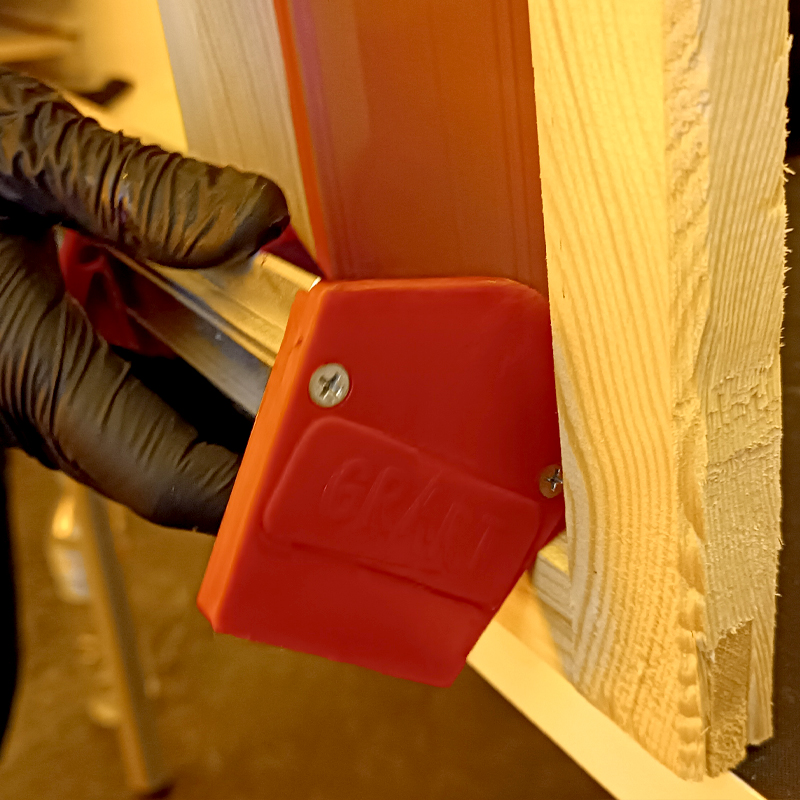
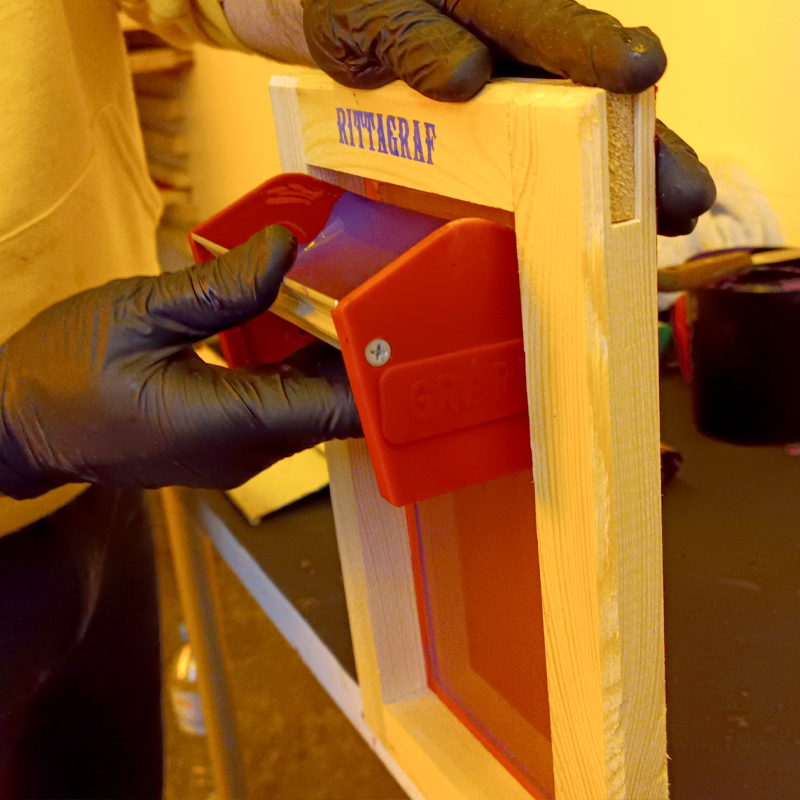
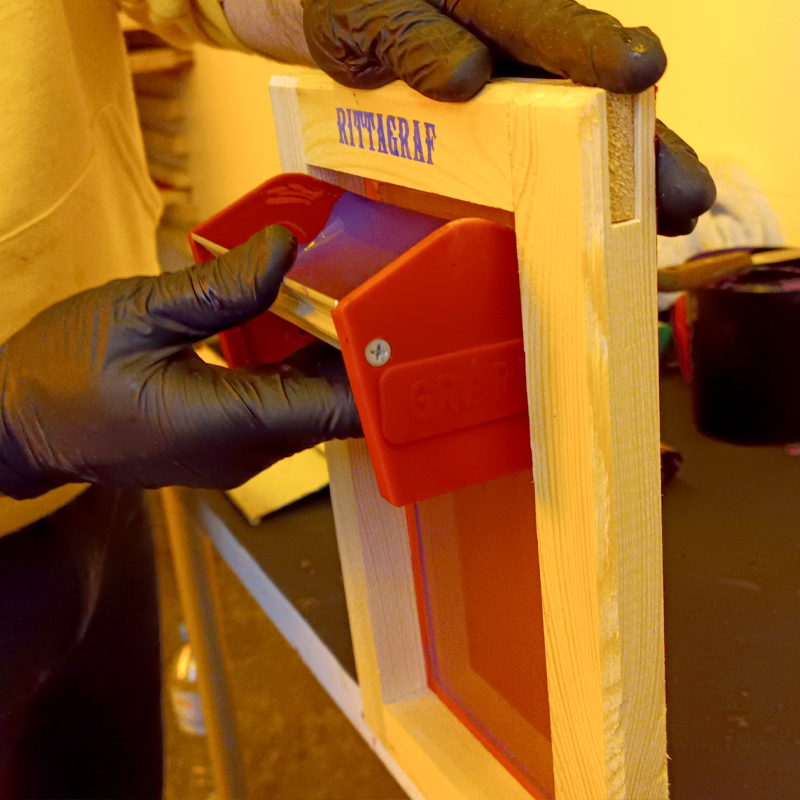
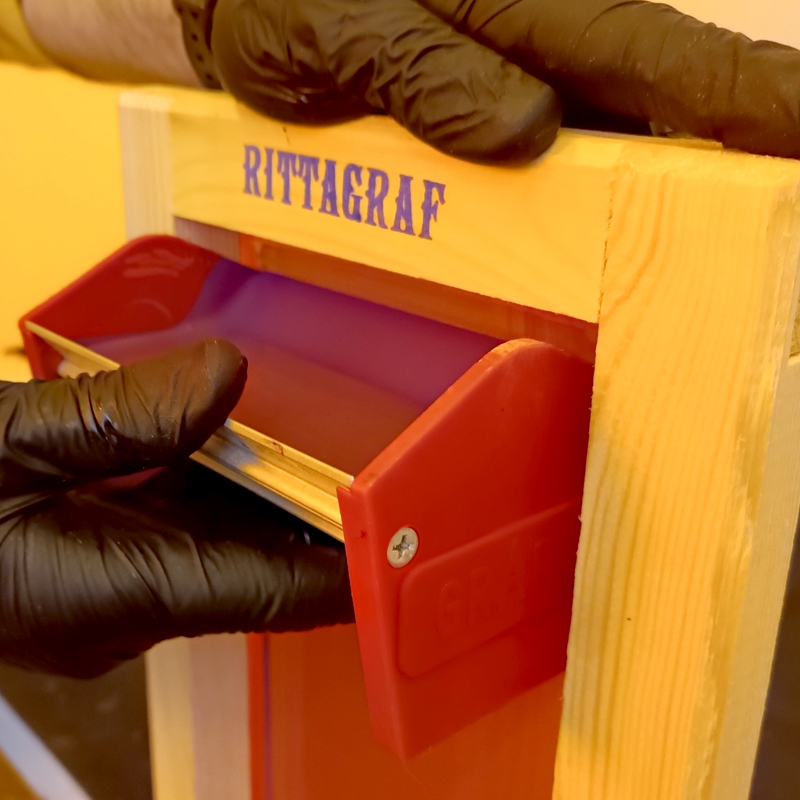
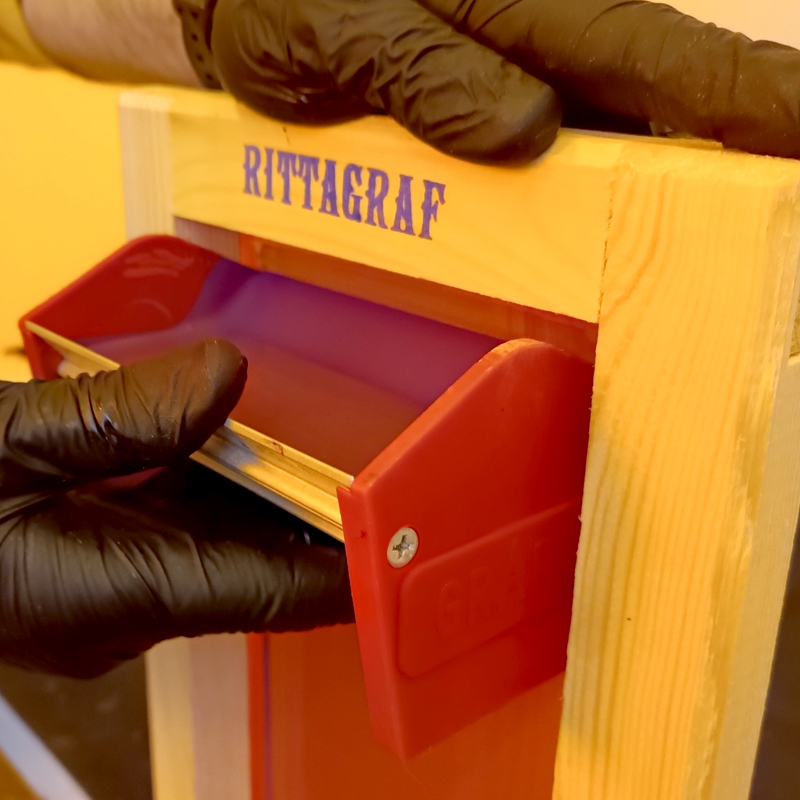
Tercera capa de emulsión por la cara interior de la pantalla (cara de racleta)
Paso 6: Recogemos la emulsión sobrante y limpiamos herramientas
Ayudándonos de una espátula, devolvemos todo el sobrante de emulsión al bote original. Es importante recoger al máximo el sobrante para evitar verter emulsión por el desagüe y aprovechar el material.
Recordamos que la emulsión es un material fotosensible y reactivo a la luz. El momento de más sensibilidad es cuando la emulsión está seca. Durante el proceso de emulsionado podemos trabajar con luz tenue pero aún así debemos proteger la emulsión lo máximo posible; cerrando el bote de emulsión, recuperando la emulsión sobrante lo más rápido posible y limpiando todos los utensilios cuanto antes.
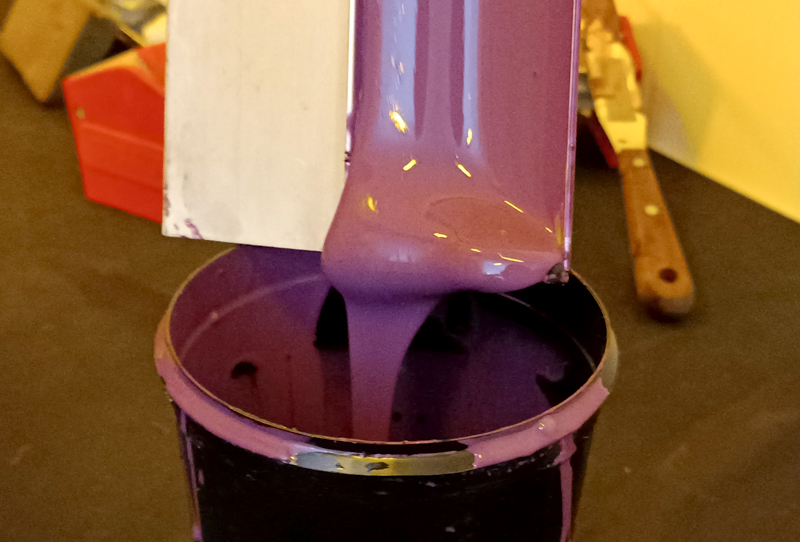
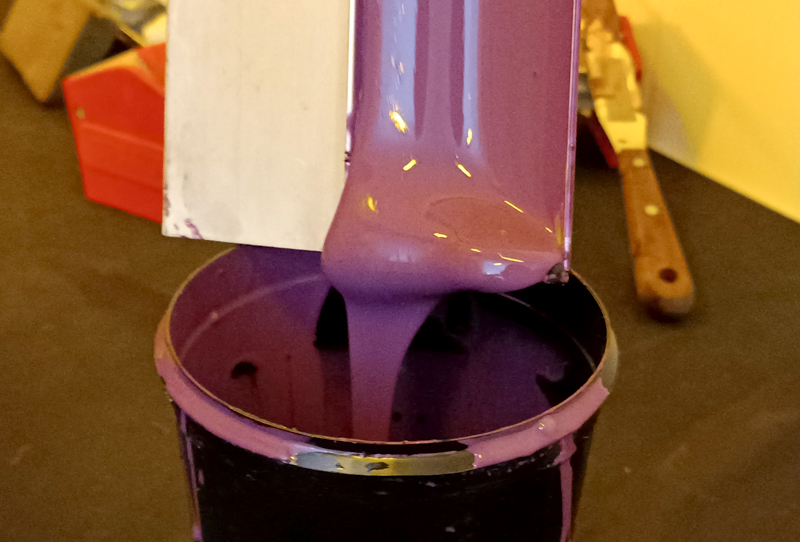
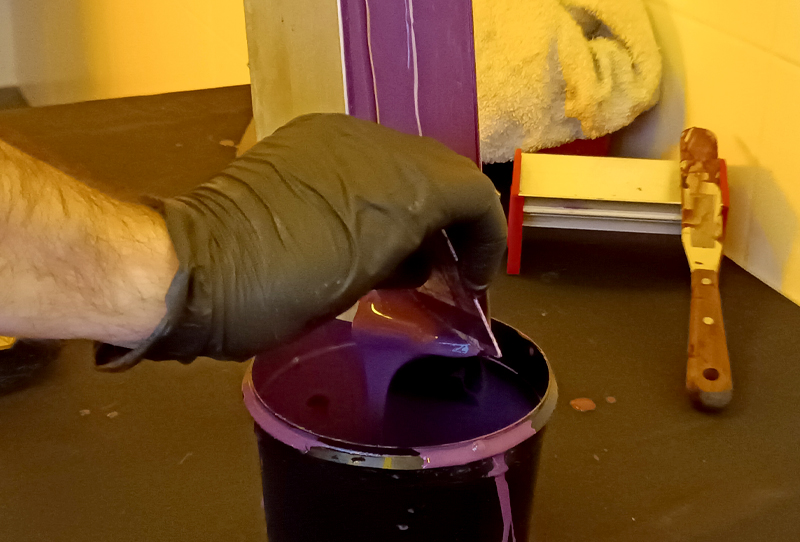
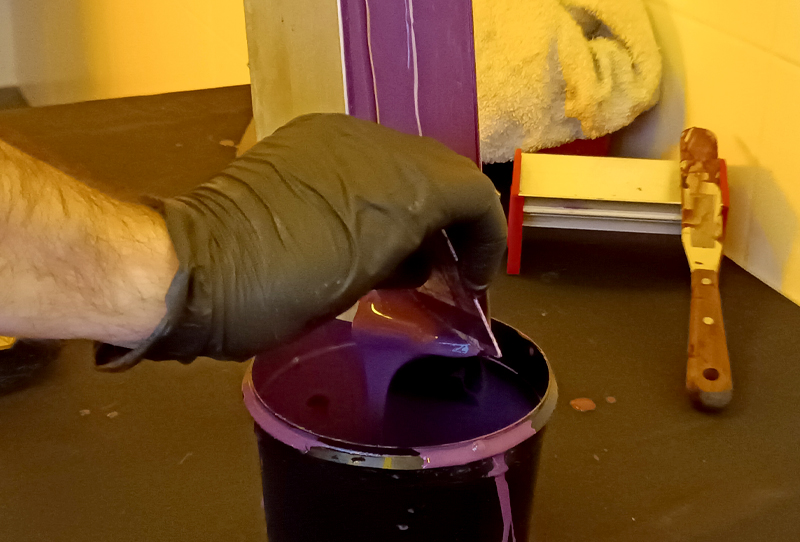
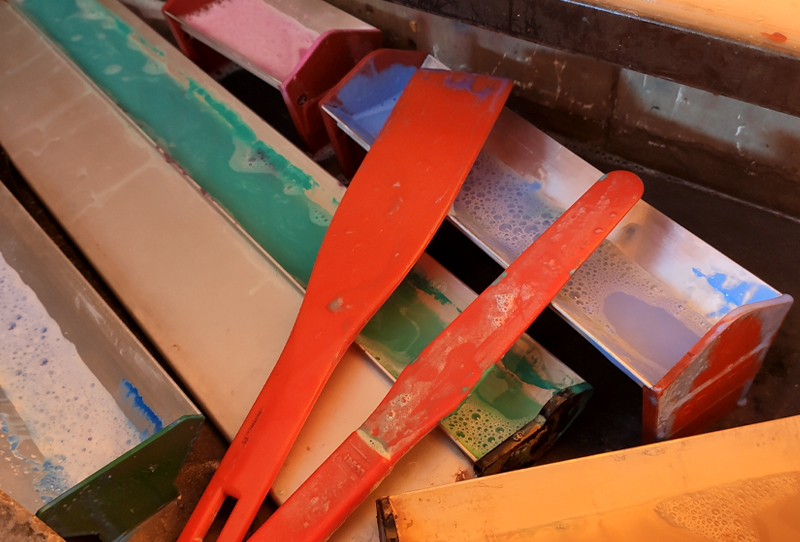
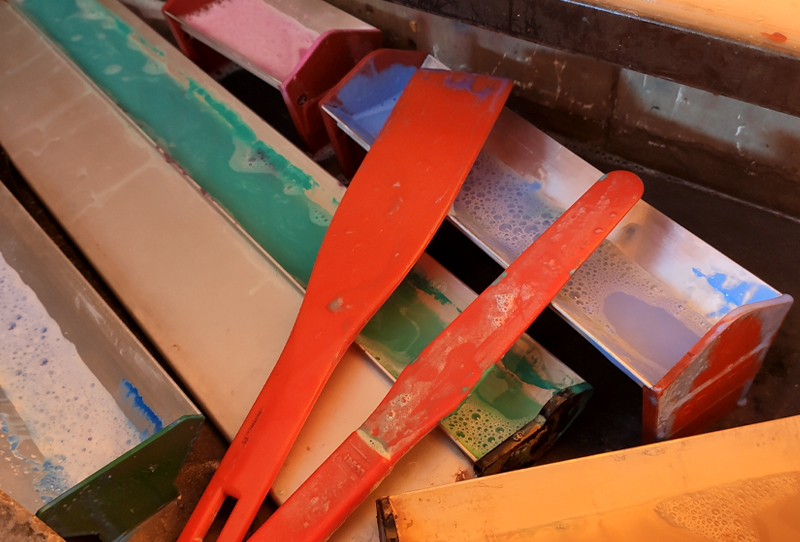
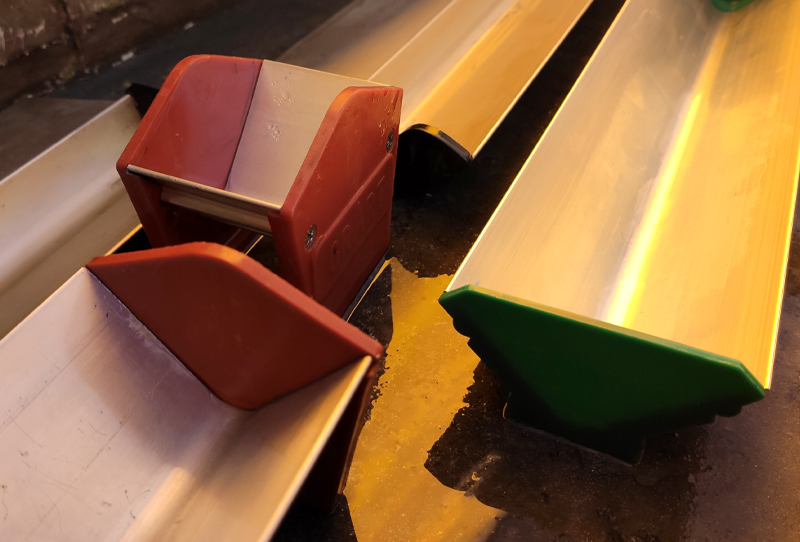
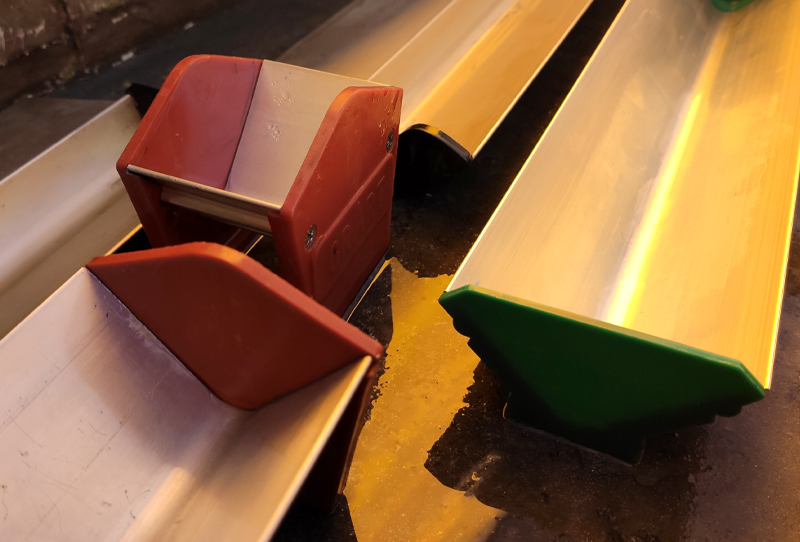
Paso 7: Secamos la emulsión en la pantalla antes de exponer
Dejaremos secar la pantalla en un lugar seco y oscuro, preferiblemente, en posición horizontal y con la parte externa (lado de impresión) hacia abajo.
Una vez que la emulsión ha secado por completo, ya tendremos la pantalla de serigrafía preparada para ser expuesta.
Aunque la emulsión esté seca, no debes tocarla nunca con las manos!, hay que evitar engrasar o ensuciar el tejido emulsionado. Una vez seca, hay que preservarla de toda fuente de luz y humedad. Si trabajas en ambientes húmedos, la emulsión puede recoger de nuevo esa humedad ambiental en el centro del marco. Es importante que esté 100% seca antes de exponer.
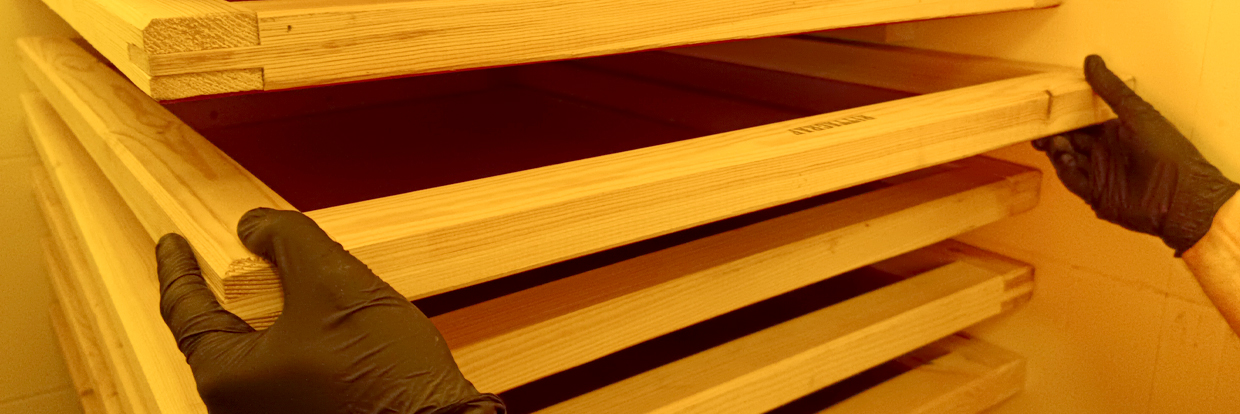
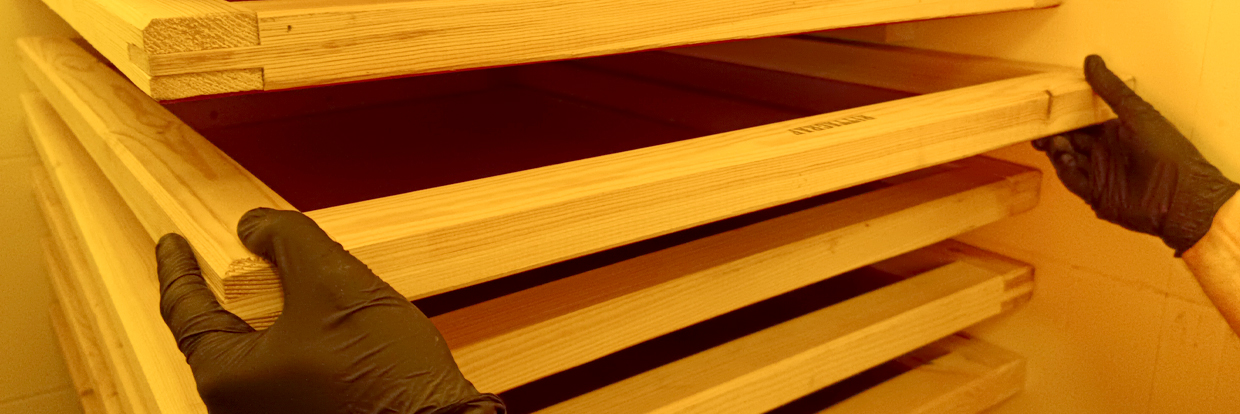
Paso 8: Estandarizar el proceso de emulsionado de pantallas de serigrafía
Para conseguir la mejor rentabilidad de la emulsión y conseguir excelentes resultados en serigrafía, es imprescindible realizar un emulsionado correcto. Todos los parámetros son importantes: el tipo de emulsión, la abertura de la malla, el filo del emulsionador, la velocidad de emulsionado, el secado, el tipo de tinta que vamos a usar, el soporte de impresión.
Haz pruebas y determina tu manera de emulsionar. Saca tus conclusiones y estandariza el proceso.
¿Te han quedado dudas sobre el emulsionado?. Visita el post en nuestro blog: Preguntas Frecuentes del Emulsionado de Serigrafía. Allí te contamos algunos tips y consejos que responden a las preguntas más frecuentes que suelen hacernos sobre el emulsionado de pantallas y marcos de serigrafía.